In the dynamic landscape of microbiology and industrial processes, the 200L Industrial Batch Fermentation Bioreactor has emerged as a cornerstone of progress and innovation. This sophisticated piece of equipment is not just a container for microbial growth; it is a meticulously engineered system that holds the key to unlocking a wide range of applications and possibilities.
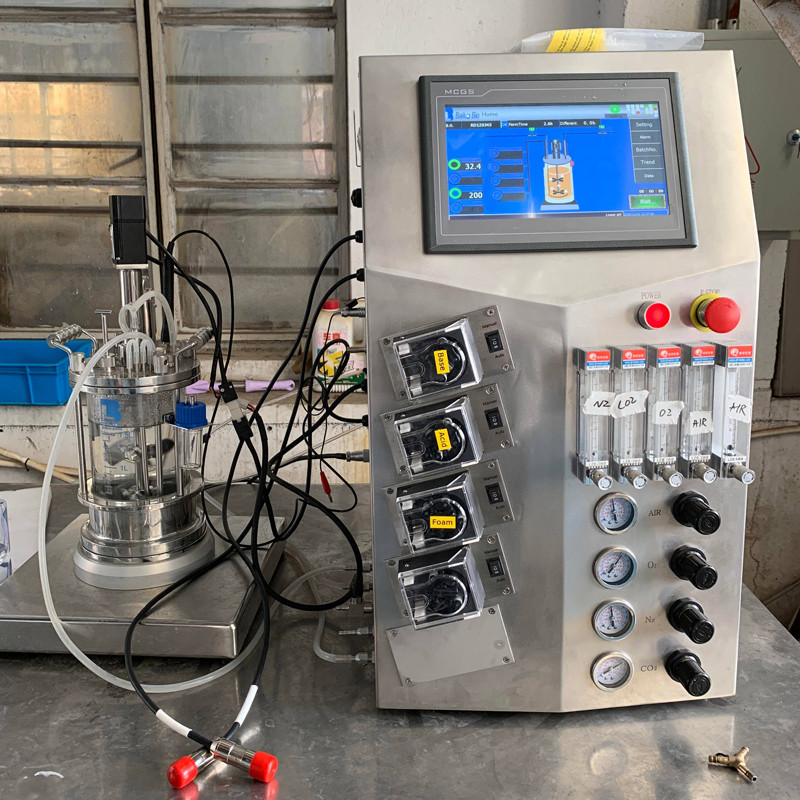
The 200L capacity of the bioreactor strikes a balance between scalability and operational efficiency. It is large enough to produce significant quantities of microbial products to meet industrial demands, yet not so large as to pose excessive challenges in terms of control, monitoring, and maintenance. This makes it an ideal choice for many mid-scale production facilities and research institutions.
One of the primary functions of the 200L Industrial Batch Fermentation Bioreactor is to provide a controlled environment for microbial cultures. The interior of the bioreactor is designed to maintain precise conditions such as temperature, pH, dissolved oxygen levels, and nutrient availability. Temperature control is crucial as it directly influences the metabolic rate and enzymatic activities of the microorganisms. Sophisticated heating and cooling systems ensure that the temperature remains within a narrow, optimal range throughout the fermentation process.
pH is another critical parameter that must be carefully regulated. Microbes have specific pH preferences for optimal growth and product formation. The bioreactor is equipped with pH sensors and mechanisms for adding acids or bases to maintain the desired pH level. Maintaining the correct pH ensures that the metabolic pathways of the microorganisms proceed smoothly, maximizing the yield of the desired products.
Dissolved oxygen is yet another vital factor. Aeration systems are incorporated to supply an adequate amount of oxygen to support the aerobic metabolism of the microorganisms. The rate of aeration is precisely controlled to avoid oxygen deprivation or excessive oxygenation, both of which can have adverse effects on microbial growth and productivity.
The supply of nutrients is also precisely managed in the bioreactor. A carefully formulated growth medium is introduced into the reactor, and its composition and concentration are adjusted to meet the specific requirements of the microbial strain being cultivated. This ensures that the microorganisms have access to all the essential nutrients they need for vigorous growth and efficient product synthesis.
The bioreactor's design also takes into account the need for efficient mixing. A well-mixed environment ensures uniform distribution of nutrients, oxygen, and heat, preventing the formation of gradients that could lead to uneven microbial growth and product formation. Agitation systems, often driven by powerful motors, are designed to provide gentle yet effective mixing without causing damage to the microbial cells.
The 200L Industrial Batch Fermentation Bioreactor finds applications in a diverse range of fields within microbiology. In the pharmaceutical industry, it is used for the production of antibiotics, vaccines, and other bioactive compounds. The controlled environment of the bioreactor enables consistent and high-quality production of these therapeutics, meeting the strict regulatory standards of the healthcare sector.
In the food and beverage industry, it plays a crucial role in the production of various fermented products such as yogurt, cheese, and alcoholic beverages. The ability to precisely control the fermentation process results in products with consistent flavor, texture, and quality.
The bioreactor is also valuable in the field of environmental microbiology. Microorganisms can be cultivated in the bioreactor to break down pollutants and perform bioremediation processes, contributing to environmental cleanup and sustainability efforts.
The operation of the 200L Industrial Batch Fermentation Bioreactor requires a high level of expertise and attention to detail. Before each batch, the bioreactor must undergo thorough sterilization to eliminate any contaminants that could interfere with the fermentation process. This involves the use of steam sterilization, chemical sterilants, or a combination of methods to ensure a sterile environment.
During the fermentation process, continuous monitoring of various parameters is essential. Advanced sensors and control systems provide real-time data on temperature, pH, dissolved oxygen, and other critical factors. Operators can make immediate adjustments based on this data to ensure the process remains on track and within the desired parameters.
Sampling ports allow for the periodic collection of small aliquots of the culture for analysis. This helps in tracking the growth of the microorganisms, assessing the progress of the fermentation, and determining the concentration of the desired products. Based on the results of these analyses, decisions can be made regarding the duration of the fermentation and any necessary adjustments to the process conditions.
Maintenance of the bioreactor is also a critical aspect to ensure its long-term reliability and performance. Components such as agitators, pumps, valves, and sensors need to be regularly inspected, cleaned, and replaced if necessary. The inner surface of the bioreactor must be maintained in a pristine condition to prevent fouling and the accumulation of residues that could affect subsequent batches.
In addition to its direct applications in production, the 200L Industrial Batch Fermentation Bioreactor also serves as a valuable tool for research and development. Scientists can use it to optimize fermentation processes, study the behavior of different microbial strains, and explore novel metabolic pathways and product formations. This research-driven approach leads to continuous improvements in microbial cultivation techniques and the development of more efficient and sustainable industrial processes.
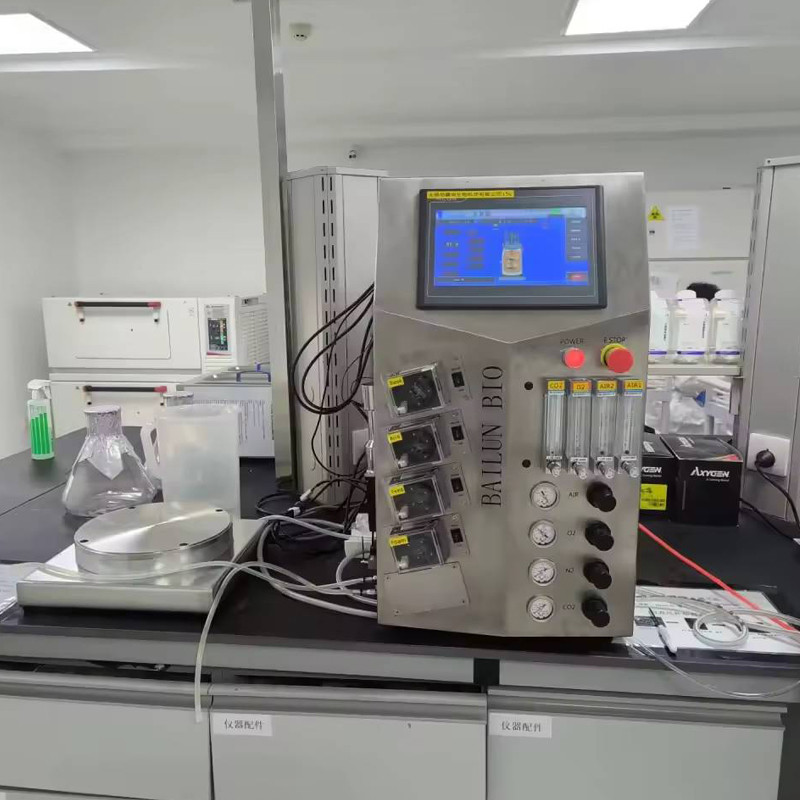
Looking forward, the 200L Industrial Batch Fermentation Bioreactor is likely to undergo further advancements and innovations. The integration of artificial intelligence and machine learning algorithms could enable more predictive and adaptive control of the fermentation process. New materials and coatings could enhance the bioreactor's durability, resistance to fouling, and ease of cleaning. Moreover, developments in sensor technology could provide even more accurate and real-time monitoring of multiple parameters within the bioreactor.
In conclusion, the 200L Industrial Batch Fermentation Bioreactor for Microbiology is a vital asset in the modern industrial and research landscape. Its ability to provide a controlled and scalable environment for microbial growth and product synthesis has made it an indispensable tool in various sectors. As technology continues to evolve, this bioreactor is set to play an even more significant role in driving innovation, improving productivity, and contributing to the development of sustainable solutions in microbiology and related fields.