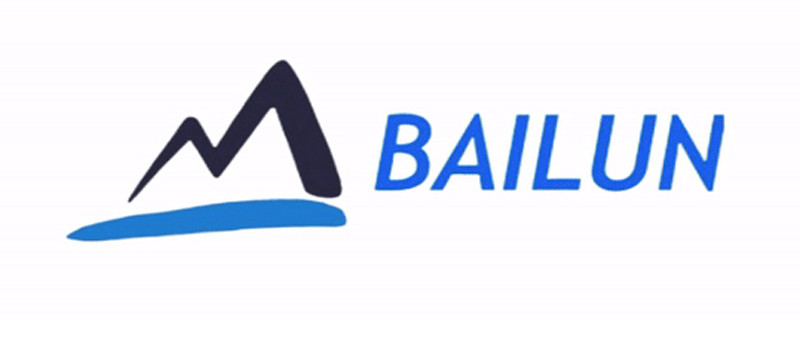
Temperature fluctuations of 1 ℃, pH deviation of 0.1, and slight fluctuations in dissolved oxygen levels - these seemingly small parameter abnormalities can result in a halving of product yield, or even render the entire batch of production useless, causing losses in the tens of millions.
Today, we will break down the three core parameters (temperature, pH, dissolved oxygen) and uncover the "fatal details" of industrial grade biological process optimization.
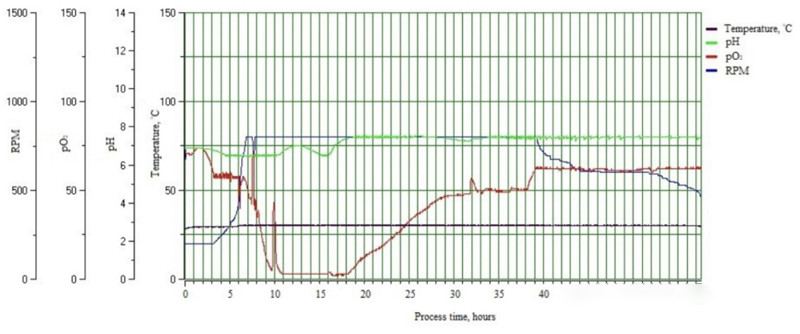
1、 Temperature: A difference of 1 ℃, the boundary between heaven and hell. The temperature control of a bioreactor is not as simple as "heating or cooling".
In mammalian cell culture, the optimal temperature is 37 ℃ (physiological temperature). Once it exceeds 38 ℃, it triggers cell apoptosis, while below 37 ℃, the metabolic rate drops sharply.
In E. coli fermentation, the induction stage needs to be lowered from 37 ℃ to 25 ℃, otherwise the formation rate of inclusion bodies will increase sharply, leading to the inability of the target protein to fold correctly.
In a real fermentation case, a certain enterprise suffered a partial overheating of 2 ℃ in the reactor due to a malfunction of the temperature control valve. Within 48 hours, 30000 liters of CHO cell culture medium were completely inactivated, resulting in a direct loss of over 20 million yuan.
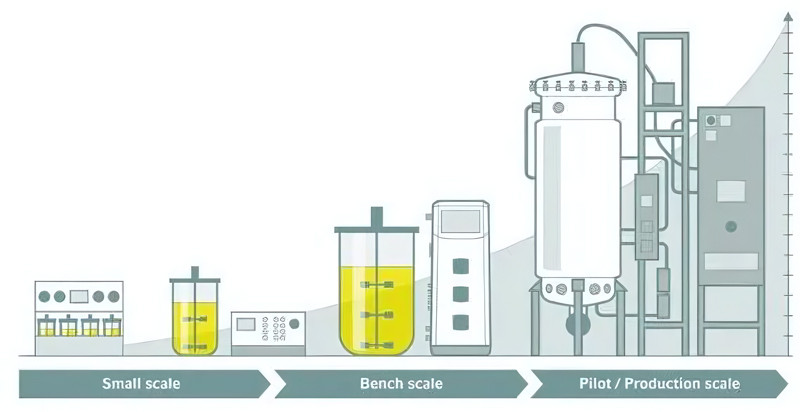
2、 PH regulation: the 'dynamic war' behind acid-base balance
Cellular metabolism continuously changes the environmental pH, and delayed regulation may trigger a chain reaction.
To ensure detection accuracy: The pH sensor of electrode potential method needs to be calibrated in real time, and an error exceeding 0.05 will cause metabolic pathway deviation.
In an extreme case, if the pH value is out of control, yeast fermentation will shift towards glycerol synthesis instead of ethanol, resulting in a 60% decrease in product yield.
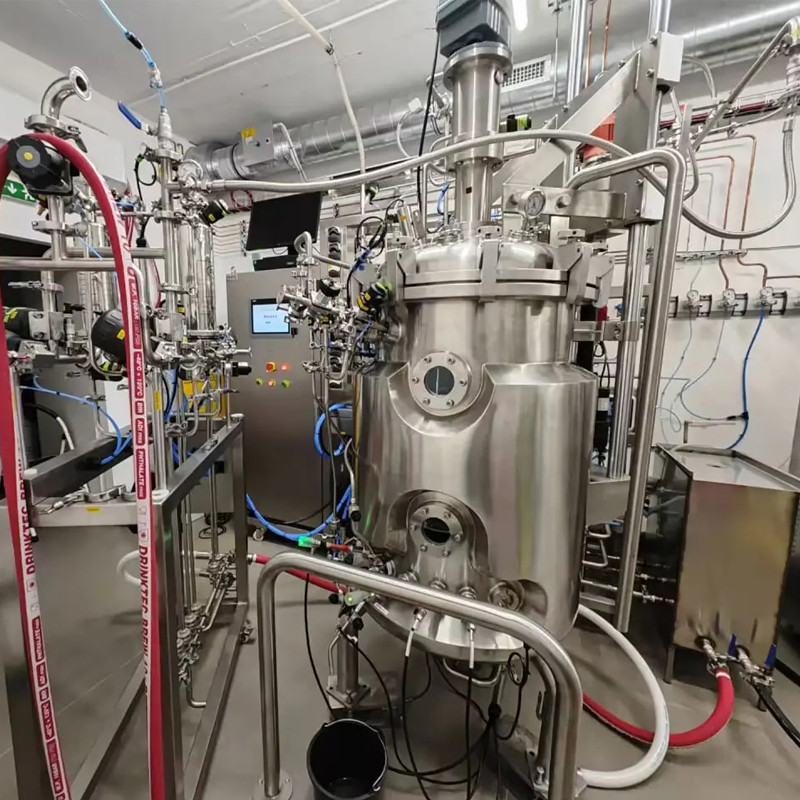
3、 Dissolved oxygen (DO): the "golden ratio" of oxygen supply
Insufficient dissolved oxygen can suffocate cells, while excessive dissolved oxygen may trigger oxidative stress. From the perspective of regulatory measures: through the coordinated control of stirring rate, ventilation rate (air or pure oxygen), and pressure.
For example, CHO cells require DO>30%, while certain anaerobic bacteria require strict oxygen limitation.
From the perspective of monitoring technology, the polarographic probe can detect DO concentration in real time, but it is susceptible to bubble interference and requires cross validation with capacitance based live cell density detection.
The current risk points include uneven stirring during large-scale production, which can lead to dissolved oxygen gradients, and local oxygen deficient areas may become "pollution hotbeds".
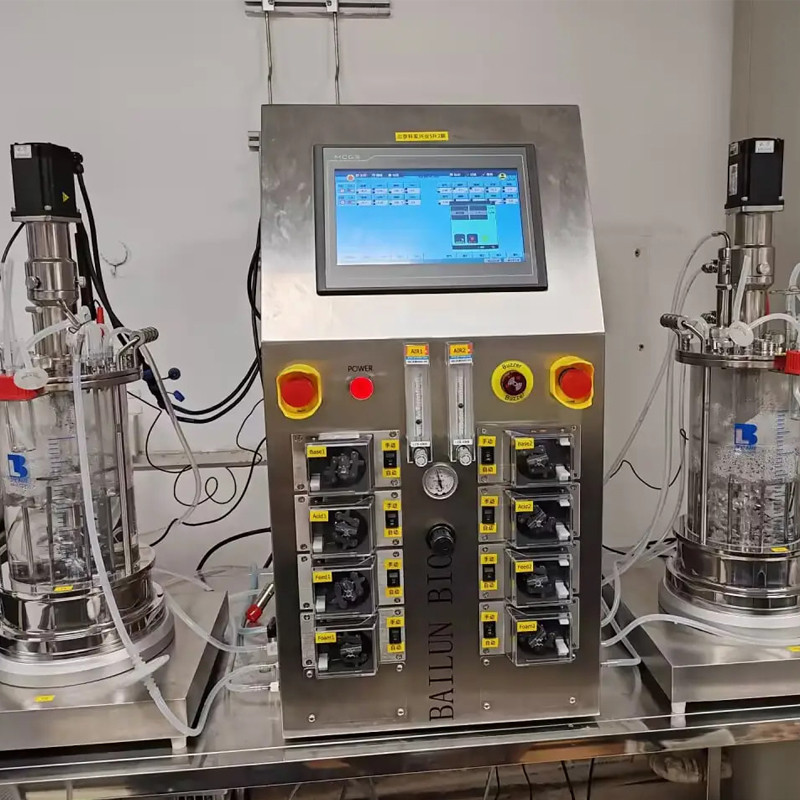
4、 How to deal with it ?
One is to fully consider the coupling effect of parameters: an increase in temperature will reduce dissolved oxygen saturation and accelerate cellular metabolism, leading to a sudden drop in pH, requiring multi parameter linkage regulation.
The second is to be wary of the scale amplification trap: the parameters of the laboratory 5L reactor and 5-ton production tank do not scale nonlinearly, for example, the difference between stirring power and dissolved oxygen transfer efficiency can reach 10 times.
The third is to use AI+big data warning modeling: for example, predicting cell growth rate based on Monod equation, combined with metabolic flux analysis (MFA) to predict risks 48 hours in advance.
Chinese bioreactors are accelerating their global expansion!
Industrial grade bioreactors are the crystallization of science, engineering, and experience. From minor temperature fluctuations to instantaneous pH shifts, each parameter is associated with tens of millions of costs and risks.
Only by deeply integrating precision sensors, intelligent algorithms, and process experience can we hold the "lifeline" of production within a millimeter.
