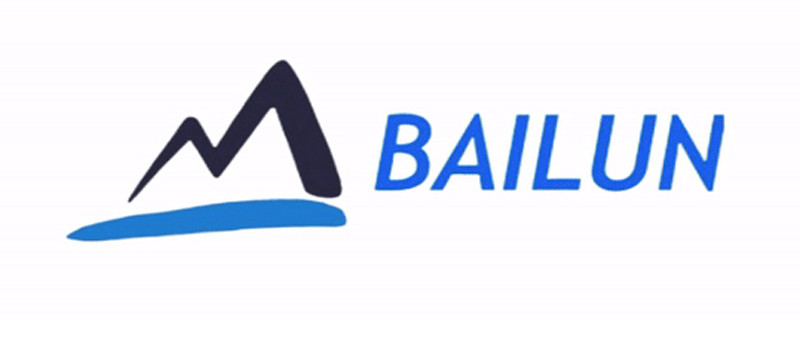
Bioreactors have become 'smart': real-time monitoring+automatic adjustment
Previously, conducting biological reactions (such as cell culture and fermentation) was like "opening a blind box": engineers adjusted the temperature and oxygen, opened the jar a few days later to see the results, and tried again if it failed.
Now, the reactor is filled with sensors and AI brains - capable of real-time monitoring of whether cells are "hungry" (glucose concentration) and "tired" (metabolic waste concentration) like a blood glucose meter, and automatically adding nutrients and adjusting temperature to keep cells in optimal condition.
For example, in the past, when producing insulin, the cells in the tank would easily "strike". Now, with the use of intelligent reactors, the production can be doubled and electricity costs can be saved by 30%.
Biopharmaceuticals begin to implement 'assembly line production'
Traditional pharmaceuticals are like "stew soup", where one pot is stewed and then another pot is stewed, which is inefficient and prone to sticking. The current trend is the "assembly line reactor": adding new raw materials to the tank while extracting the finished product, with 24-hour uninterrupted production.
The benefits are a 70% reduction in reactor volume (saving factory space), a 40% reduction in production costs, and no need to clean equipment every batch (saving water and time).
For example, the production of COVID-19 vaccine can expand to 1 billion doses in three months.
Cross border environmental protection of bioreactors
Do you think bioreactors can only be used for pharmaceuticals? Even garbage treatment plants are currently in use. Waste gas treatment: using microorganisms to 'eat' factory odors (such as benzene from paint factories), purification efficiency of 90%
Wastewater purification: Cultivate "oil eating bacteria" in the reactor to treat oily wastewater in 3 hours, with a cost only 1/5 of chemical methods
The temperature difference of 1 ℃ in the bioreactor has caused the enterprise to lose millions?
Disposable reactor: the "takeaway box" in the pharmaceutical industry
Traditional stainless steel reactors are like "big iron pots" that need to be washed once for 3 days. Nowadays, disposable plastic reactors are popular: open the bag and use it immediately, dispose of it after use (materials can be recycled)
Suitable for small-scale production, such as customized anti-cancer drugs and rare disease drugs
How much money can be saved? Building a traditional pharmaceutical factory costs 1 billion yuan, using disposable equipment costs only 100 million yuan, and can also switch to different drugs at any time.
To summarize
Bioreactors are becoming smarter (with automatic regulation), more efficient (with assembly lines), and more cross-border (even with exhaust pipes).
The logic behind it is threefold - to make cells feel refreshed, to reduce costs, and to keep the earth cool.